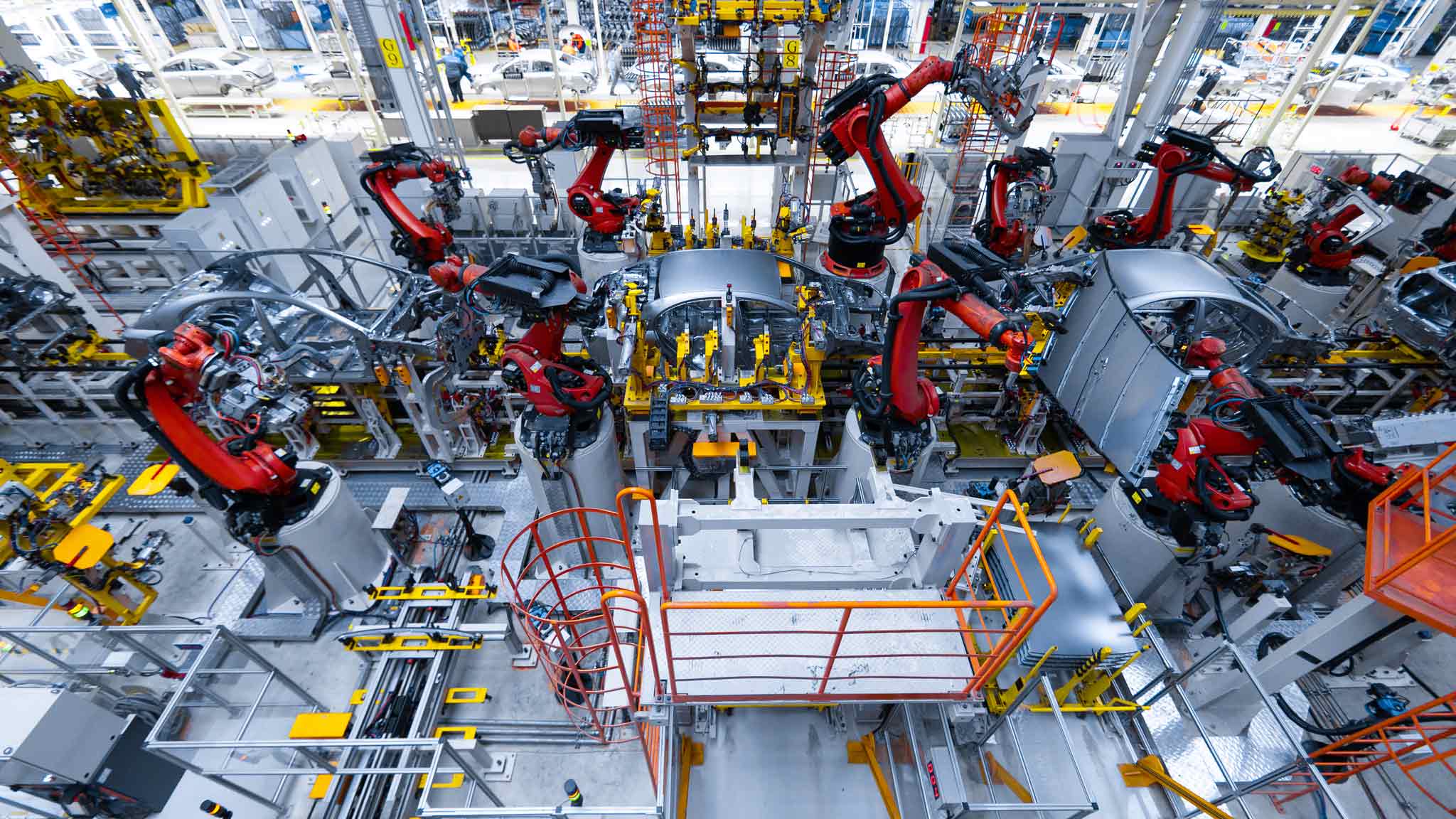
Even as recently as a few years ago plant efficiency was often measured through metrics tied only to the production process. While production is still the primary focus, progressive manufacturers are now looking more closely at the systems supporting production, such as base-building HVAC and lighting controls to more closely monitor energy consumption and carbon emissions, security cameras that can capture usable video in real-time, and digital access control to help keep key areas of the plant secure.
Once former stand-alone equipment has been connected through central DDC (direct digital control) using open communication protocols like BACnet and MQTT, the data from this equipment can be made available to track performance over time and share with other stakeholders to help meet Industry 4.0 and/or Net-zero targets. It can also alert to anywhere in the world when adverse conditions arise that may impact safety, production, QA/QC or other KPIs.
In addition to gaining the ability to operate this newly connected equipment more efficiently in terms of run-time, temperature set-points, negative/positive pressure through better exhaust fan control, etc., there may be incentives from gas and electric utilities to help enhance the project’s ROI, though take note that these incentive applications must be submitted to your local utilities in advance of awarding the project(s).
Manufacturing plants, most with office areas attached, often run on stand-alone control for mechanical HVAC, lighting and central systems like compressed air with limited central visibility for Plant and Maintenance Managers and other stakeholders. Other plants may have some HVAC equipment controlled through central DDC (direct digital control) that is reaching end-of-life and may be due for replacement.
If this describes your situation, you’re debating whether new base-building controls will provide a return on investment (ROI) that meets your company’s hurdle rate. Consider these additional factors that often lie outside the typical ROI calculation (typical ROI is between 12% and 19% of base-building energy consumption (electricity and natural gas)) when introducing DDC into a stand-alone HVAC control condition.
When executed properly by a qualified building technology integrator, you may be surprised by the added value that comes out of an upgrade to a new central Building Automation System (BAS), including the following:
- Complete visibility of controlled equipment through your computer or mobile device, including real-time alerts on conditions that are important to various stakeholders.
- Open communication protocols like Open BACnet and MQTT allowing data to be securely shared for use by the entire organization to help meet KPIs relating to production, Industry 4.0, Net-zero or other initiatives.
- Full point-to-point recommissioning on all controlled equipment. While “commissioning” to some means flipping a switch and watching for sparks, when properly executed in a mechanical HVAC controls setting, it means that every point on every piece of controlled equipment is verified for proper function and control. The value-add of true commissioning is that previously undiscovered faults on existing equipment are often brought to light, potentially enhancing equipment longevity, energy efficiency and comfort.
- Utility incentives can be significant. By involving representatives from your gas and electricity provider early in the process, they can help to quantify incentives that could move the needle significantly on your ROI calculations. In the coming years some utilities are at risk of reaching full peak demand capacity on their existing infrastructure and they’ll pay generous incentives to help you to reduce your peak demand load on their distribution systems.
Most plant managers have been tasked with reducing costs and meeting corporate energy and carbon reduction targets, all while modernizing their facilities. Would a careful approach to upgrading base-building controls in your plant and office spaces help you to advance in all of these areas?